ITR Undercarriage Parts
In cooperation with USCO, a global corporation undergoing rapid development, we can supply the market with the broadest assortment of undercarriage parts of superior quality, for which our business partners can also rely on the Renomag professional servicing support.
The production line of ITR tracked undercarriages is fully controlled within the company, from the procurement of raw materials to the final inspection, together with the intermediate stages of component designing, machining, heat treating and assembling. Multiple quality inspections of purchased ore and steel make the best use of expertise and rich experience covering metallurgical processes and materials.
DEVELOPMENT AND DESIGN
The ITR components of tracked undercarriages are developed and designed by the R&D and other technical departments of USCO using the CAD systems of computerized design and cooperating with partner universities.
The engineering and R&D departments located in Italy, South Korea and China are in constant communication with each other and share their engineering studies, technologies and competences.
MANUFACTURE
The forging operations are performed on the company's own premises at a new production plant offering 35,000 m2 of floor space and equipped with forging presses 1,600 tonnes and 2,500 tonnes. The foundry, covering 30,000 m2 inside a production plant sized 54,000 m2, has the yearly casting capacity of 10,000 tonnes. To meet the most demanding international standards and requirements from the OEM manufacturers, the production uses a range of heat treating and mechanical machining processes.
QUALITY
The products are developed and optimized in cooperation with the Section for Machine Production & Structural Analyses of the Modena University and the Reggio Emilia University.
All the manufacturing plants have laboratories and testing premises where materials undergo a range of different quality tests and checks before and after they are utilized for production purposes. The tests are conducted internally on own premises in accordance with the international standards and using pre-calibrated instruments designed specifically to guarantee the consistency or results.
CHAINS OF TRACK SHOES
ITR chains can serve to a large group of machines of different makes and applications, and are also available in a range of varied configurations, specifically:
- non-lubricated without sealing
- non-lubricated with steel sealing
- greased with polyurethane sealing
- oil-lubricated with sealing and oil charge
ITR chain links, made of forged boronated steel which gives them outstanding resistance to wear, have a runner Rockwell C50 hardened to a depth of 8 to 12 millimeters or deeper, in dependence on the link size.
Split master links for lubricated chains are made by the process of electric discharge machining (EDM). The process of manufacturing the ITR connecting links is protected by a patent licensed to USCO.
The technology of overall and differential hardening used to manufacture the bushings is intended to produce cores of high resistance, optimal surface hardness and resistance to wear.
The procedure employed to manufacture pins has intentionally been developed so as to guarantee high durability and ductility in the pin core, while maintaining the pin's external girth able to withstand wear & tear.
The oil- and grease-lubricated chains have the "ALL WEATHER" sealings, elements differently designed to suit their anticipated applications. The PREMIUM chains are characteristic of new sealing sets developed to meet the most stringent quality standards as required for rigorous applications. Shapes and materials of the sealings ensure their excellent oil retaining capacity and improve the lubrication of surfaces between the pin and its bushing.
The line of ITR brand chains will suit a range of machines, from mini-excavators to mining machines.
TRACK SHOES
The line of ITR brand track shoes will suit any application:
- single-, double- or triple-rib shoes;
- standard and reinforced shoes for tough applications;
- special shoes
ROLLERS
The lower track rollers and the upper carrier rollers of the ITR brand for excavators and bulldozers are designed to withstand the most demanding operations and conditions. The ITR company supplies a broad range of types and sizes for all common makes and models of machinery. The ITR rollers and other top-quality components are manufactured, forged and high-ductility cast from chosen raw materials, e.g. boronated steel.
The ITR rollers are in-depth hardened and precision machined to guarantee consistent quality. Their robust assembly, lifelong lubrication and quality control throughout the process of manufacture and after, ensure the rollers will operate reliably.
The rows of lower track rollers and upper carrier rollers are designed for manifold applications - from mini-excavators over bulldozers to mining machines.
IDLER WHEELS
Front idlers of the ITR brand are manufactured by the most innovative techniques of designing and machining. They are made of high-quality steel and treated to special heat processing so that they offer excellent performance in the most exacting conditions. The ITR idler wheels are fitted with sealings of advanced design and their method of manufacture satisfies the most stringent specifications applicable in the trade. They are assembled on production lines with direct oil charging.
The ITR track idlers can be chosen in several different configurations:
- idler body alone;
- idler with bushings and shaft;
- idler with collars;
- idler with fork;
- idler with tensioning unit;
The line of ITR idlers used to guide the track is designed for manifold applications - from mini-excavators, dozers to mining excavators.
SEGMENT GROUPS
The ITR sprockets and segment groups are suitable for a broad range of crawlers and their driving units. The manufacturing process includes die forging, machining and deep hardening with an emphasis on achieving maximum service life.
Groups of segments are available in a wide assortment and typically used for bulldozers.
SPROCKETS
The sprockets are cast, machined and heat treated. They can be used for excavators as well as machines whose applications and/or tracked undercarriages are similar to excavators.
The line of sprocket - driving wheels is designed for manifold applications - from mini-excavators to machines in quarries and mining.
PRINCIPLE APPLICATIONS
The line of ITR tracked undercarriages is the most comprehensive group of such products on the market. Together with a full-scope series of components for tracked undercarriages, the products are designed to suit not only standard excavators and bulldozers but also asphalt layers and drilling units together with deforestation and agricultural machinery. The flexibility of manufacture and extensive designing expertise are the reasons why the ITR brand of undercarriages comes as the first choice when ordering "customized" products for clients with specific needs.
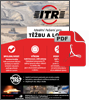
ITR Mines and Quarries Renomag (394 KB)